Introduction
Inventory management is considered a fundamental building block to a company’s longevity.
If you run a general contracting company, a sub-construction company specializing in specific trades, or even a service professional, your inventory is everywhere. Not paying extra attention to your inventory management may result in major issues with your business. What you may not know is that inventory is a far more complicated area than it seems.
As the construction industry moves rapidly towards digitization, is your company still using logbooks and spreadsheets to track and manage your inventory? An outdated inventory management system consumes a lot more physical resources and workforce. Such time consuming and painstaking inventory method does not give you the standard of functionality and service that an automated solution offers.
Learn more here.
Table of Contents
What Is Construction Inventory Management?
Generally, inventory management is the process of organizing, ordering, stocking, tracking, and utilizing a business’s inventory— regardless of what the items could be. It is a complex and highly essential aspect of supply chain control and management, mainly when your business includes a broad category of inventory items in large quantities distributed in multiple locations or warehouses.
Even though inventory management may seem overwhelming at first glance, selecting a consistent and reliable inventory management system to track all your company’s possessions can save you huge chunks and resources, such as time, money, and even unnecessary stress. Always remember that there are various innovative tools and technology available that can cut you hours off your daily, monthly, and even annual activities— and inventory management is one of them.
Key Inventory Management Terms
To properly familiarize yourself and your team in terms of organizing your inventory management procedures, here are standard inventory-control techniques you can utilize in your own company.
1. Economic Order Quantity
Economic order quantity (EOQ) is a formula for the ideal quantity of order a company needs to purchase for its inventory with a fixed set of variables like demand rate, total production costs, and other factors.
The primary goal of EOQ is to minimize the related costs a construction company typically incurs. The formula is used to identify the maximum number of product units to minimize buying frequency. Additionally, the formula also takes several units in the delivery and storing of inventory unit costs. This can help free up the budget in inventory for most construction companies.
2. Minimum Order Quantity
The minimum order quantity (MOQ) is the smallest amount of set stock a supplier is willing to sell on the market for the supplier side. If your company’s procurement team cannot reach the MOQ of a specific material, the supplier won’t sell it to you.
For example, inventory materials that cost more to produce usually have smaller MOQ as opposed to cheaper materials that are easier and more cost-effective to produce.
3. ABC Analysis
This popular categorization technique split subjects into three categories to identify items that significantly impact the overall inventory cost.
Category A: this serves as your most valuable product that can contribute the most to your overall profit.
Category B: refers to the products that fall somewhere between the most valuable to the least important.
Category C: indicates the small transactions vital for the overall profits but don’t weigh much individually in your company altogether.
4. Just-In-Time Inventory Management
JIT inventory management is a method that arranges and organizes raw materials orders from suppliers in direct connection to the supplier’s production schedules.
JIT is an excellent way to reduce inventory costs. Construction companies receive inventory on an “as-needed” basis rather than ordering too much and risking dead stock of materials. Deadstock refers to the inventory that was never sold or used by the customers before being removed from the sale status.
5. Safety Risk Inventory
Safety risk inventory (or SSI) management refers to the extra inventory being ordered in addition to the expected demand. This technique is frequently implemented to prevent stockouts typically brought by unforeseen customer demand changes or incorrect forecasting.
6. FIFO and LIFO
First-In-First-Out (FIFO) and Last-In-First-Out (LIFO) are methods used to determine inventory’s overall cost. FIFO assumes that the old inventory is sold first, which aims to keep the inventory safe.
On the other hand, LIFO assumes that the newer items in the inventory are typically sold first. Moreover, it helps prevent inventory from going bad or deteriorated.
7. Reorder Point Formula
This inventory management technique is based on a company’s sales and purchase cycles that vary on a per-product basis. A reorder point formula is usually higher than a safety number on stock to factor in lead time in the production.
8. Batch Tracking
Batch tracking is one of the most conventionally used quality control inventory management methods wherein companies can group, arrange, and monitor a set of stocks with similar traits or functions. This technique helps track the expiration of inventory or easily trace the defective items back to their original batches.
9. Perpetual Inventory Management
The most common inventory management trick in the book, perpetual inventory management, is simply counting the items as soon as they arrive. Being the most basic technique, it can be recorded manually using pen and paper or a spreadsheet.
10. Dropshipping
Dropshipping is a fulfillment method in inventory management in which a supplier doesn’t keep the products it sells in stock. When a supplier makes a sale, rather than picking it from their inventory, they purchase the specific item from a third party and have it shipped to the customer. The supplier or seller never sees or touches the product itself.
11. Lean Manufacturing
Lean management is a broad set of practices applicable to any business practice, even in the construction industry. Lean manufacturing aims to improve efficiency by eliminating non-valueadding activities and removing unessential activities from a daily business.
12. Six Sigma
Six sigma is the infamous brand of teaching that gives companies tools to enhance their business’s performance by boosting profit and decreasing the growth of excess inventory.
13. Lean Six Sigma
This type of six sigma method is more advanced by focusing more on increasing the word standardization used on a daily basis and enhancing the flow of business.
14. Demand Forecasting
A familiar inventory management technique to suppliers, demand forecasting, is based on a company’s historical sales data to formulate an accurate estimate of customer demand’s expected forecast in the future. Ultimately, an estimate of the goods or services a company expects their customer to purchase in the future.
15. Cross-Docking
Cross-docking is a management system for inventory whereby an incoming truck unloads items supplies directly into the outbound tracks to create a just-in-time (JIT) shipping process. There is a little to entirely no storage left in between deliveries.
16. Bulk Shipments
Lastly, bulk shipments are a cost-efficient technique of shipping when you palletize inventory more than once.
Common Inventory Mistakes to Avoid
When your inventory is organized correctly, you can expect the rest of the supply-chain management to fall into place. However, without it, you risk your company to a litany of mistakes like out of stocks, mis-shipments, mis-picks, overstock, and so on. Proper inventory management is critical and can be considered a baseline a project could have and key to solving this problem.
1. Mis-picks
Mis-picks are brought about by disorganized shelf labels. Incorrect paper pick lists, or just a messy warehouse in general.
2. Mis-shipments
These are results from mis-picks at the start of the inventory process and can also result from the lack of quality control and quality assurance procedures.
3. Out of stocks and overstocks
happens when a company incorporates manual methods to place orders without keeping an updated quantity or a full grasp of the state of their supply inventory. This is a lousy predictor for inventory forecasting and concludes in too little or too much stock. The latter means a delay in the construction activities, while the former means money down the drain.
All of these inventory mistakes will cost you valuable resources in construction– time and money– and costs you wasted labor that will be spent in correcting the errors in the future. When you fail to implement inventory management tools, the risk of human mistakes increases by the minute. Additionally, your customer service reviews and loyalty take a negative turn as well.
What Is Inventory Cycle Process?
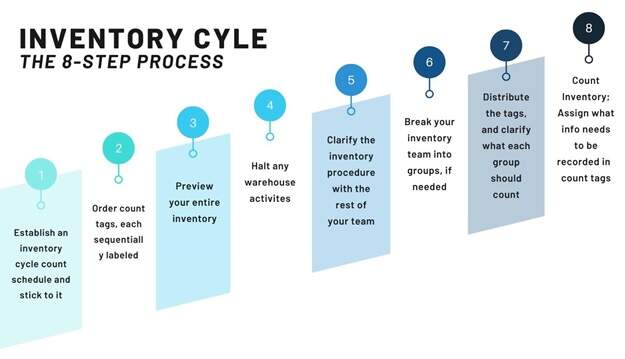
An inventory cycle count is a tried and tested strategy in managing construction inventory that involves counting a specific subset of its entirety on a particular date, at a particular time, consistently, and repeating intervals. Also referred to as cycle count and cycle counting, the inventory cycle count, is a reliable way of tracking inventory and determining overall inventory value.
For example, suppose you own general contractor business. In that case, you might inventory all your building materials at your headquarters every 15th day of the month and your construction tools and equipment at your central warehouse every first week of a new quarter.
This is what creating an inventory count schedule looks like.
Construction inventory counting is a fusion of art and science, and you and your construction team will get better and faster in conducting these cycle counts over time.
Generally, the main objective of cycle counting is to keep tabs on a company’s inventory by counting a specific subset of inventory at fixed and regularly scheduled intervals. Typically, an annual audit of every little thing a company owns and keeps in stock often requires businesses to close for a day or two, which is seldom performed to prevent inventory loss. The purpose of inventory count is to offer businesses a valuable and efficient alternative to time-consuming and costly inventory counts.
You may also encounter an inventory cycle count known as inventory cycle audit as well.
Now that you have determined which inventory items require the most attention, you can now proceed to the cycle count of your physical inventory using the tips mentioned earlier. To further help you implement Inventory Cycle Process to your construction business, here is a step-by-step process for beginners to recommend that you try out.
- Establish an inventory cycle count schedule, and make sure to stick to it.
- Order count tags, each sequentially labeled, so you can accurately track your inventory. 3. Preview your entire inventory. Have a good perspective of all the things that you will organize.
- Halt any warehouse activities. During inventory count, no item should be removed or restocked.
- Clarify the inventory procedure with the rest of your team, so there is no confusion once you started.
- Break your inventory team into groups, if needed.
- Distribute the tags, and clarify what each group should count, respectively.
- Count inventory. Usually, one team will do the manual labor of counting all the physical items, and the other party is tasked to record the findings. You can personally assign what information needs to be recorded in the count tags.
Three Inventory Management Systems
Ever since it has been widely known the importance of inventory management systems in any industry, there has been a rise in several types of the management process— at a variety of costs as well— available for companies of all shapes and sizes. From a high-level and professionally designed inventory management software to the traditional sheet and paper duo, there are many ways to track all the inventory items you have on hand.
1. Pen and Paper Inventory Management
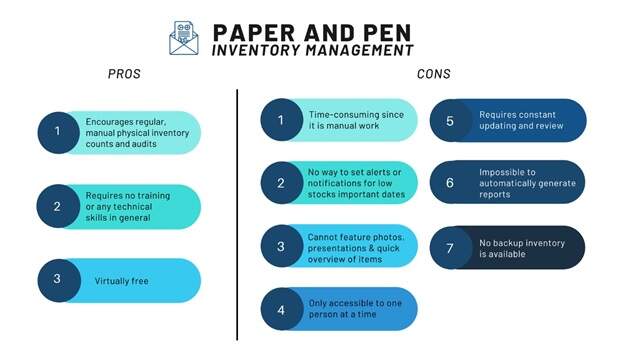
Manually managing construction inventory using a little more than a sheet of paper is the oldest trick in the book that has been used for centuries by our ancestors. It’s old-fashioned but potentially can be an effective way of keeping track of the inventory that you have in stock. Of course, such a system is extremely limited in terms of the items you can manage all at once and works best for businesses that keep stock of just a few things and employ just a handful of people.
Below are some of the pros of pen and paper inventory management:
- Encourages regular, manual physical inventory counts and audits
- Requires no training or any technical skills in general
- Virtually free
Now, here are some of the cons of using pen and paper for your inventory processes:
- Very time-consuming since it is manual work
- No way to set alerts or notifications for low stocks and important dates such as reorder or deliveries
- Cannot feature photos, visual presentation, and quick overview of the items
- Only accessible to one person at a time – Requires constant updating and review
- Impossible to automatically generate reports to gather inventory information forecast, or understand the figure
- Once these paper documents are lost, no backup inventory is available. Your data is lost forever.
2. Spreadsheet Inventory Management
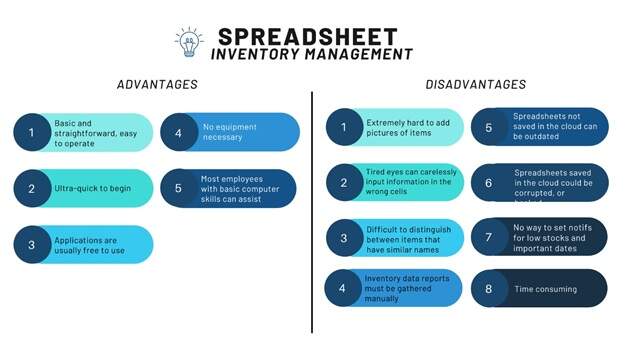
Generally, an inventory spreadsheet helps you keep track of all the details in your inventory, including little too critical information such as item name, category, SKU, location, condition, quantity, estimated value, purchase amount, condition, and expiration date.
You can easily access inventory spreadsheet templates online, or you can quickly create your own using products like the infamous Microsoft Excel, Google Sheets for online editing, and Numbers for Mac IOS users. If you opt to create your inventory in a spreadsheet in any of these applications, add a column for every little information you would like to track. Don’t forget to leave a few open-ended cells for random notes and reminders.
Ideally, you should save the template of your inventory spreadsheet in your first tab. This is so it can be easily accessed when you print it out and fill it in when you take the inventory manually. After this, create another tab every time you conduct a physical inventory and properly date the tab. This way, you will be able to gather information quickly about your overall inventory over time. Familiarize yourself with the essential formulas and ratios so you could easily calculate your date when needed.
But of course, an inventory management system via spreadsheet has its advantages and disadvantages too.
- Below are some of the advantages of using an inventory sheet:
- Basic and straightforward, easy to operate
- Ultra-quick to begin
- Applications are usually free to use
- No equipment necessary
- Most employees with basic computer skills can assist
On the other hand, here are the disadvantages of an inventory spreadsheet:
- Extremely hard to add pictures of items
- Tired eyes can carelessly input information in the wrong cells or jumble data
- Difficult to distinguish between items that have similar names
- Inventory data reports must be gathered manually
- Spreadsheets not saved in the cloud can be outdated or impossible to access on gadgets
- Spreadsheets saved in the cloud could be corrupted, altered, or worse, hacked
- No way to set alerts or notifications for low stocks and important dates such as reorder or deliveries
- Time consuming, as inventory must be taken first and then recorded later at the computer
3. Inventory Management Software
Ultimately, all inventory management software the most crucial information about a company’s inventory. This can include the item location, stock levels, minimum stock required, and purchase amount. Inventory management software also helps companies, both big and small, save valuable resources such as time, money, and even unwanted stress by incorporating modern technology and automated inventory management systems designed for your business needs.
There is a wide array of inventory management software available in the market that you can choose from. Some of this software is highly technical, very expensive, incredibly difficult to operate, and not industry-specific. However, most companies discover that inventory software that costs them huge bucks a year (or even more) still doesn’t work to make their inventory management much more bearable and less overwhelming.
Ten Ways You Can Benefit From Cloud-Based Inventory Management
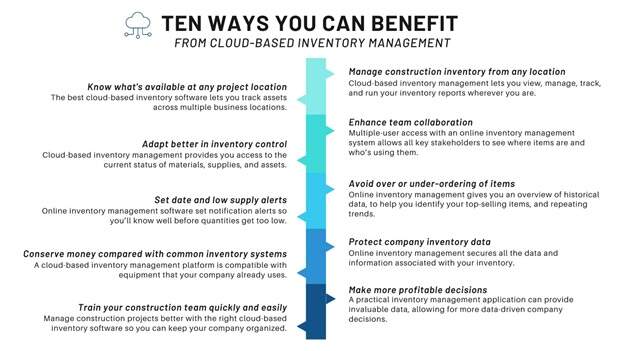
Think your company is too new—or too invested in spreadsheets—for cloud-based inventory? Here are ten reasons to consider another look at this cutting-edge, forthcoming, and proven approach to inventory management.
1. Manage construction inventory from any location
Cloud-based inventory management lets you view, manage, track, and run your inventory reports wherever you are, whether that’s on a job site, in an office, at a client meeting, traveling in your truck, or working from home.
No matter what services your company offers, inventory management software gives you a real-time status of your inventory items on hand. While on a call with a customer, you can access your web-based inventory and tell them how many disposal quantities you have in stock and when they will be delivered to your warehouse. Information is at your fingertips. Let me ask you: what’s more empowering than that?
2. Know what’s available at any project location
The best cloud-based inventory software lets you track assets across multiple business locations, such as different job sites or warehouses, and enables you to categorize inventory items efficiently as needed.
With web-based inventory software, if you are a general contractor with building materials scattered in five project locations throughout the New York City area, you’ll still be able to view inventory at every location. That way, when one project job site needs a main door lockset, you can check your existing stock across the company in your online database before buying (and waiting for) new deliveries.
Efficiencies like this help construction companies save money, avoid unnecessary stress, and keep customers happy, too. An easy triple win.
3. Enhance team collaboration
Multiple-user access with an online inventory management system allows all key stakeholders to see where items are and who’s using them. Inventory apps you’re your company improve internal logistics and ensure that items are available to project teams that use the most.
If you are a plumbing subcontractor company that supplies PVC pipes across the California area, cloud inventory software can help track supplies and materials. You can quickly identify which of your shops use larger PVC pipes, see what colors are in demand by customers, and have the right amount of them stocked at the suitable locations.
4. Adapt better in inventory control
Cloud-based inventory management provides you access to the current status of materials, supplies, and assets. IT construction department, for example, must accurately track thousands of valuable company assets to prevent data loss or theft. Inventory management software powered by the cloud can ensure this information is safe, secure, and accessible if any questions or concerns arise.
5. Avoid over or under-ordering of items
Online inventory management gives you an overview of historical data to help you identify your top-selling items, peak demand seasons, and repeating trends. Reliable inventory control eliminates guesswork and avoids waste caused by over-ordering items or supplies that you don’t need and your customers don’t want.
However, under-ordering affects business profits, too. If you regularly under-order to avoid waste but frequently sold out of items, your clients will shop elsewhere, or your employees will be forced to stop working and wait for materials to arrive. Cloud-based inventory software helps you order items with precision so no inventory item or customer can slip from your fingers.
6. Set date and low supply alerts
With an online inventory management software, you can set notification alerts so you’ll know well before quantities get too low- which we know is dangerous for companies. And you can schedule a date— low-stock triggered instant notifications for important reminders, like ordering plenty of Personal Protective Equipment (PPE) for your warehouse employees.
7. Protect company inventory data
Online inventory management secures all the data and information associated with your inventory. Updating activity of any kind is immediately stored and backed up. Cloud inventory storage preserves status and protects it from mistaken deletion and loss, theft, corruption, or cyber threats.
If you need information about your inventory immediately, you don’t have to look for one sheet of paper that’s nowhere to be found. Also, you don’t have to worry about your computer and files going haywire, frying all your saved spreadsheet in the process. And if your inventory contains confidential or sensitive information, you can rest assured that it is safe and secure in the cloud.
8. Conserve money compared with common inventory systems
A traditional inventory system, like paper-and-pen and Excel spreadsheets, can cost thousands. However, a cloud-based inventory management platform is compatible with equipment that your company already uses—desktops, laptops, mobile devices—and you can try it today.
Additionally, some online inventory software is already incorporated with other digital features that can also help your business, such as project task tracking and construction schedule. All you need to do is find the best project management software best suited for your company’s needs to help you automate tasks, which means less manual work and saved expenses.
9. Make more profitable decisions.
A practical inventory management application can provide invaluable data, allowing for more data-driven company decisions. For example, with a more informed understanding of the supply and demand of your inventory, you can go some way to forecast trends, giving you a more competitive edge over other construction companies.
Additionally, with the additional ability to work out your inventory turnover rate, you will also identify possible opportunities to reduce the amount of inventory you are holding in your warehouses and project locations and lower your inventory carrying costs.
10. Train your construction team quickly and easily
Don’t have a week (or even a day) to learn how to use your new inventory management software? You’re in luck. You can learn how to use most of them in minutes, as cloud-based inventory management applications are intuitive. Your construction team can quickly take advantage of the software’s features without reading a 10-page back-to-back user manual that is too technical and hard to understand.
Managing inventory isn’t especially fun, but it’s highly essential. Manage construction projects better with the right cloud-based inventory software so you can keep your company organized, profitable, and ready for growth—all without breaking a sweat.
How Pro Crew Schedule Can Help Your Construction Company
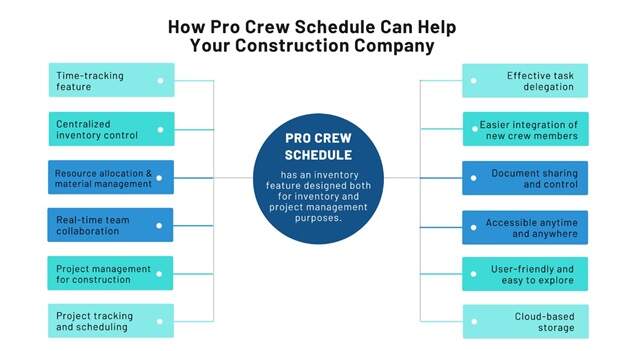
Many construction companies want a simple interface simultaneously, intuitive web-based inventory software that streamlines the time-consuming parts of inventory management so they could focus on more important and urgent tasks at hand. At the end of the day, companies want a tool that would make their operations more straightforward and not more complex than it already is.
One of the significant factors that can be attributed to construction companies’ productivity is how well they manage their tools, equipment, and materials. These resources are considered significant investments for construction companies, so it is highly crucial to track than more cost-effectively and productively. Exploiting any shortcuts and loopholes when dealing with inventory can make your company vulnerable to costly damages in the long run.
Adopting cloud-based construction management software, like Pro Crew Schedule, allows construction firms to make plans for upcoming projects both logically and financially, ensuring that materials in circulation can be optimized optimally.
Pro Crew Schedule has an inventory feature enabling you to visually track all of your construction equipment, tools and even supplies. Such a system allows you to see which worker has certain pieces of equipment or tools, deliver instant reports and give you complete details of an item. Pro Crew Schedule has an inventory feature designed both for inventory and project management purposes.
- Time-tracking feature
- Centralized inventory control
- Resource allocation and material management
- Real-time team collaboration
- Project management for construction
- Project tracking and scheduling
- Effective task delegation
- Easier integration of new crew members
- Document sharing and control
- Accessible anytime and anywhere
- User-friendly and easy to explore
- Cloud-based storage
Transfer all counting data into construction inventory software to ensure that all your data is stored and can be accessed anytime, anywhere.